Pacifiers sold in the United States are subject to strict safety standards and chemical restrictions. There are also requirements concerning labeling, certification, and testing of pacifiers.
This guide serves as an introduction to these requirements. More specifically, we take a closer look at CPSIA, 16 CFR Part 1511, 16 CFR Part 1303, and other requirements that tend to be relevant to pacifiers manufactured or imported for the US market.
Content Overview
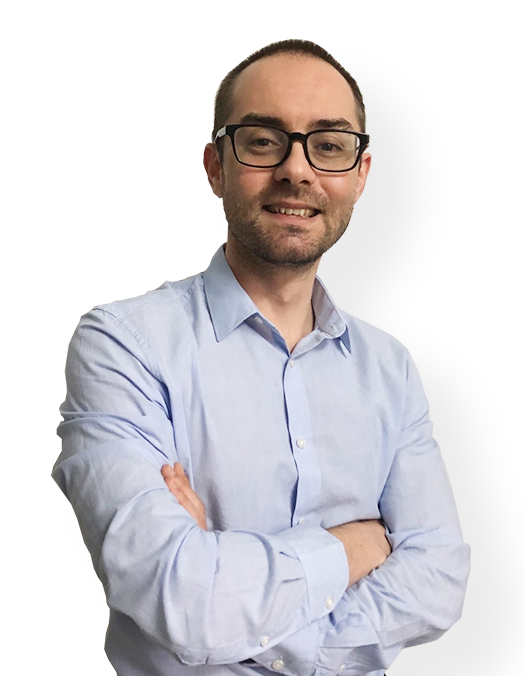
FREE CONSULTATION CALL (US, EU & UK)
- Request a free 30-minute call with Ivan Malloci to learn how we can help you with:
- Find product requirements
- Certification and labeling
- Lab testing
Consumer Product Safety Improvement Act (CPSIA)
The CPSIA regulates children’s products, which include pacifiers. The CPSC’s Pacifiers Business Guidance defines a pacifier as a product that:
- Has a nipple for young children to suck on
- Is not meant to help babies obtain fluid
- Usually has a handle or ring; and
- Usually includes a guard or shield
Standards
The Pacifiers Business Guidance explains that pacifiers are subject to the requirements of the following parts and standards:
a. 16 CFR Part 1511 – Requirements for Pacifiers
b. 16 CFR Part 1303 – Ban of Lead-Containing Paint and Certain Consumer Products Bearing Lead-Containing Paint
c. 16 CFR 1307 – Prohibition of Children’s Toys and Child Care Articles Containing Specified Phthalates
d. 16 CFR Part 1500.87 – Children’s products containing lead: inaccessible component parts
e. ASTM F963 – Standard Consumer Safety Specification for Toy Safety
We explain the main requirements below in this article.
Other requirements
General CPSIA requirements, such as the following, also apply to pacifiers:
- Children’s Product Certificate (CPC)
- CPSIA Tracking Label
- Testing carried out by a CPSC-accepted lab
16 CFR Part 1511 – Requirements for Pacifiers
16 CFR Part 1511 sets out pacifier requirements, including physical properties, testing, and labeling. The goal is to ensure that pacifiers are safe to use, even after wear and tear.
Guard or shield requirements
Subpart 1511.3 sets out performances and design requirements for the guard or shield of the pacifier, which includes the following:
- Alignment
- Tensile force
- Ventilation holes
- Dimension
For instance, the pacifier guard or shield should contain at least two ventilation holes with specific dimensions and alignments.
Protrusions requirements
Subpart 1511.4 specifies the protrusion requirements for pacifiers. In particular, no protrusion from the face of the shield opposite to the nipple should exceed 0.63 inches (or 16 mm). It also provides protrusion testing requirements.
Structural integrity tests
Subpart 1511.5 specifies the structural integrity test requirements for pacifiers’ nipples, handles, and other parts. It also specifies heat cycle deterioration procedures, which require pacifiers to be submerged in boiling water repeatedly before the tests.
The goal is to assess how much force is needed to break the components into small parts, to ensure that no young children can break the product and ingest the newly created small parts.
Ban on ribbons, strings, cords, or other attachments
Subpart 1511.6 forbids the sale of pacifiers that include any of the following features or materials:
- Ribbons
- Strings
- Cords
- Chains
- Twines
- Leather
- Yarn
Labeling requirements
Subpart 1511.7 requires the packaging of pacifiers to bear a warning statement. The warning statement must be visible, legible and have the following wording:
“Warning – Do Not Tie Pacifier Around Child’s Neck as it Presents a Strangulation Danger.”
16 CFR Part 1303 – Ban of Lead-Containing Paint and Certain Consumer Products Bearing Lead-Containing Paint
16 CFR Part 1303 covers toys and other products meant for children to use. This includes pacifiers.
Specifically, it bans children’s products – and other products – that contain more than 0.006% of lead in paint and other similar surface coating materials.
16 CFR Part 1500.87 – Children’s products containing lead: inaccessible component parts
16 Part 1500.87 sets lead limit requirements for children’s products. As such, accessible components of pacifiers should not contain more than 100 ppm (parts per million) of lead.
A component is considered inaccessible if:
a. It is not exposed to the user due to a sealed covering or casing, and
b. It does not get exposed under foreseeable use and abuse
16 CFR Part 1307 – Prohibition of Children’s Toys and Child Care Articles Containing Specified Phthalates
16 CFR Part 1307 bans the importation, manufacture, distribution, and sale of childcare products – including pacifiers, – and toys that contain more than 0.1% of the following phthalates:
- DEHP
- DBP
- BBP
- DIBP
- DPENP
- DHEXP
- DCHP
ASTM F963 – Standard Consumer Safety Specification for Toy Safety
Section 4.20 of ASTM F963 sets requirements for pacifiers. According to the Pacifiers Business Guidance page, these requirements include the following:
a. Rubber nipples must adhere to the specified nitrosamine restrictions
b. Pacifiers must comply with the heavy metals limits set in section 4.3.5
Pacifier Clips: Physical Requirements
According to the CPSC’s Pacifier Business Guidance, 16 CFR Part 1501 – Method for Identifying Toys and Other Articles Intended for Use by Children Under 3 Years of Age Which Present Choking, Aspiration, or Ingestion Hazards Because of Small Parts covers pacifier clips.
Specifically, 16 CFR Part 1501 provides a method to identify products that contain small parts, which are banned in products intended for children under 3 years. Note that this part exempts pacifiers because 16 CFR Part 1511 already sets small parts requirements.
Additionally, the CPSC recommends pacifier clips to be shorter than 7 to 8 inches.
Toxic Substances Control Act (TSCA)
The TSCA sets requirements regarding the manufacture, importation, usage, and disposal of certain substances and mixtures, as well as products that contain those substances.
Below, we briefly explain two parts of the Act that may be relevant to pacifiers.
40 CFR Part 705: PFAS
40 CFR Part 705 sets reporting and recordkeeping requirements regarding PFAS, which – per the EPA – can be found in plastics.
Specifically, this part requires companies to specify whether reportable amounts of PFAS are present in their products.
40 CFR Part 751: PBT Substances
40 CFR Part 751 regulates certain persistent, bioaccumulative, and toxic (PBT) substances. PBT substances, such as decaBDE, can be found in plastic products, which might include pacifiers.
For example, it bans the manufacturing, processing, and distribution of:
- DecaBDE-containing products
- PIP (3:1)-containing products
Country of Origin Marking
As per 19 CFR Part 134, a Country of Origin Marking is required for consumer products sold in the US – including pacifiers and their packaging.
This part sets several labeling provisions, including the following:
- Placement
- Method of marking
- Wording of marking
It also set exemptions for some of the requirements.
California Proposition 65
California Proposition 65 restricts substances such as phthalates and heavy metals in consumer products for sale in California.
Here we list several examples of substances on the Proposition 65 List that might be found in pacifiers:
- BBP
- DEHP
- DIDP
- DBP
- DnHP
- DINP
- BPA
If your product contains any restricted substance above the set limits, a warning label is required
Lab Testing
You must ensure that your pacifiers comply with the physical and chemical requirements of relevant regulations and standards, and you do this by having your products lab tested. These tests may include:
a. Chemical tests – for example ensure that pacifier doesn’t contain phthalates or other restricted substances above the limits
b. Mechanical tests – for instance to make sure that the pacifier cannot easily break into small parts that a child can ingest
c. Physical tests – for example ensuring that a pacifier clip is not too long, as this may cause strangulation hazards
When your product passes testing, you receive a test report that proves your product’s compliance with the relevant requirements.
Test methods
We list here several test methods and procedures found in the standards mentioned previously in this article:
- Protrusion tests
- Structural integrity tests
- Use and abuse tests
- Size testing
CPSC accepted labs
Third-party labs must be accepted by the CPSC to be able to provide valid test reports for pacifiers or other children’s products. Further, third-party testing is mandatory in the US for all pacifiers, and other children’s products.
Here we list several CPSC-accepted labs that can test pacifiers against the requirements set by 16 CFR Part 1511:
- Bureau Veritas
- Eurofins
- Intertek
- QIMA
- SGS
- TÜV Rheinland
- TÜV SÜD
- UL
You can find more labs on the CPSC website.
Compliance risks
Not all pacifiers manufactured outside the US are designed and manufactured to comply with 16 CFR Part 1511, and the other requirements mentioned in this guide. In practice, this means that some pacifiers are unsafe and non-compliant with the requirements that concern physical and mechanical properties.
Pacifiers can pose choking hazards, meaning there is zero margin for error.
It is critical to ensure that the pacifier is designed to comply with the relevant safety principles – and that does not happen by accident. In other words, you must have a profound understanding of how 16 CFR Part 1511 and other mechanical safety standards directly impact the design and construction of pacifiers before you enter production.
Further, shield and teat materials can contain excessive amounts of phthalates, lead, and other restricted substances. Ultimately, the safety of the design and the materials must be verified through lab testing.