Product testing is often required when importing products to the United States, European Union, Australia, Canada, and other countries. However, many importers struggle to understand how and when to submit product samples to the testing company.
In this guide, I explain how this process works and whether you should submit pre-production samples or batch samples or testing.
Content Overview
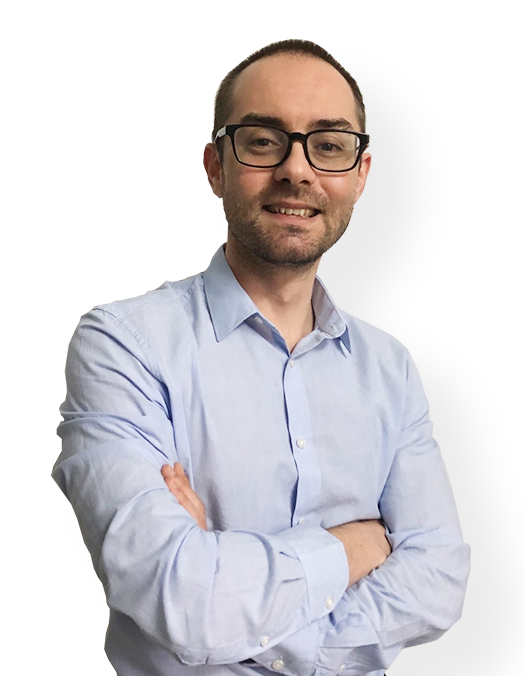
FREE CONSULTATION CALL (US, EU & UK)
- Request a free 30-minute call with Ivan Malloci to learn how we can help you with:
- Find product requirements
- Certification and labeling
- Lab testing
Why is third-party lab testing necessary?
Most consumer products sold in the United States, Europe, Australia, and many other countries are regulated to some extent. Chemicals and heavy metals regulations, such as REACH and CA Prop 65 apply to essentially all consumer products. For some products, including electronics and children’s products, additional safety standards apply.
Most manufacturers and buyers have the expertise and equipment required to verify if a product or material is compliant – which is why third-party lab testing is necessary.
At what stage should I get my product lab tested?
How and when you submit product samples largely depends on which stage of the process that third-party lab testing is necessary. There are a few scenarios to take into consideration:
Electronics
It’s necessary to verify compliance with electrical safety standards and electromagnetic compatibility before the product goes into mass production.
As such, the pre-production samples/prototypes should be tested. Further, the risk of compliance issues is low if the pre-production sample/prototype passes the testing – as the prototype and final mass-produced products are made using the exact same components.
Toys & Children’s Products
Toy safety and children’s product safety regulations often require that products collected from the production run/batch are lab tested. The reasoning behind this is that the compliance of the materials and design properties of the final product sold on the market is what matters.
On the other hand, you might not want to enter mass production before you’ve tested the pre-production samples – as you may otherwise end up with a batch of non-compliant products that you must scrap. As such, it’s sometimes necessary to test both the pre-production samples and samples collected from the production run. That is, however, costly.
Material Samples
Materials used to make product samples, such as clothing and accessories, are not always matching the materials used to make the final product. It’s, therefore, more common to skip pre-production sample testing and submit production run samples.
That said, make sure you withhold the balance payment and refrain from booking a shipment until the test results are in.
How do I prepare the booking?
The first step of the process is to request a quotation from a testing company, such as QIMA. This can be done online, and you’ll need to provide this information:
- Product type (e.g. Earphones)
- Manufacturing country (e.g. China)
- Destination country/market (e.g. the United States)
- Age group (e.g. Adults)
The testing company can then assess applicable regulations and testing standards, on which the quotation is based on. The testing company normally also provide the following information:
- Delivery address
- Number of required samples*
- Booking number**
Number of required samples
*Product testing companies often need more than one product sample. In some cases, they need 5 to 10 units to carry out testing. As such, pre-production sample testing may not be an option, as you may simply not have enough product samples or material required for the testing process.
Booking number
**The booking number must be clearly written on the parcel. Otherwise, the testing company cannot identify the product samples upon arrival.
Product Sample Submission
Here’s an overview of different options for submitting product samples from the factory to your lab testing company.
Option A: Submit pre-production samples directly to the testing company
Once completed, product samples are normally submitted to the buyer to undergo a quality evaluation. As a buyer, you can now book lab testing and submit samples directly to the testing company. The benefit is that you’ll know that the ‘right product’ is being tested, which is something you can’t always take for granted.
Option B: Instruct your supplier to submit production run samples to the testing company
Another option is to ask your supplier to submit the product or material samples directly, which is fairly common when it comes to batch product lab testing. The benefit is that you’ll save time. Most major testing companies have labs in Mainland China and other Asian countries, where your factory is most likely located.
As such, you don’t need to get your product sent halfway across the world and then back – which you probably don’t have time for as you wait for the test result before you can approve the shipment.
However, this also increases the risk of the supplier sending a compliant sample, made to pass lab testing – while your products are not. This is a serious risk that should be taken into consideration when this could result in major fines or forced product recall.
Option C: Instruct your quality inspector to submit production run samples to the testing company
Rather than taking the risk of allowing your supplier to submit product samples, instruct your quality inspection agency to collect batch samples for you. Doing so drastically reduces the risk testing ‘designed for compliance’ product samples, while you’ll also save precious time.
In addition, many product testing companies also offer quality inspection services. As such, they’ll simply collect samples and take back to their testing facility in one go.
This also makes the submission process a breeze, as you don’t have to instruct your supplier on how to correctly mark the booking number and the sample quantity to submit.
How can consumers ensure the products they purchase are compliant with safety regulations and free from harmful substances?