Electronic product compliance goes beyond listing safety standards and paperwork. Ensuring compliance when importing, exporting or manufacturing electronic devices starts at the drawing board.
In this article, Fabien Gaussorgues of Sofeast Limited in Shenzhen, shares his profound technical expertise and explains what electronic product compliance really means in practice.
Content Overview
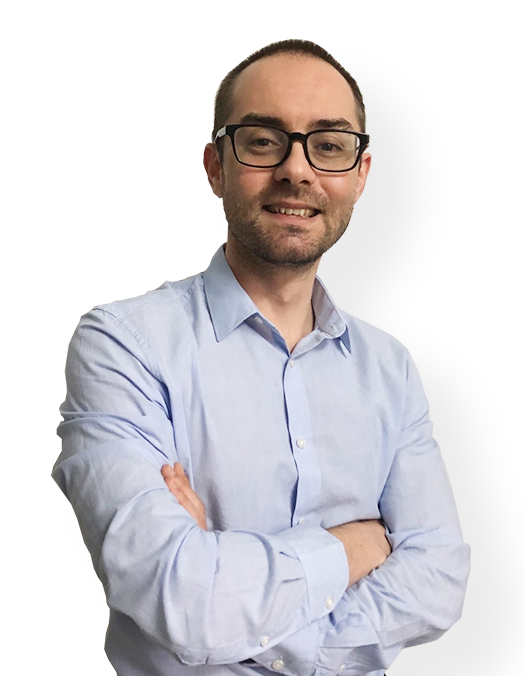
FREE CONSULTATION CALL (US, EU & UK)
- Request a free 30-minute call with Ivan Malloci to learn how we can help you with:
- Find product requirements
- Certification and labeling
- Lab testing
How do you normally assess which electronics standards and regulations apply to a product?
To generalize the very start of a New Product Specifications Development, the initial design requirements document would show what problem the product is going to solve and high-level product expectations that will be experienced directly or indirectly by the end-user. This document would also have design constraints such as size, weight, and major functionalities.
So now we have a starting point, it is time to start designing the product, this needs to be broken down into different components and documents such as:
- Mechanical structure (e.g. a plastic case)
- Electronic design
- Assembly
- Hardware requirements
- User Interface (UI/UX if required)
- System integration if product is integrated
- Material considerations like recycling
- Safety regulations (RoHS, CE, FCC)
You also need to consider the ease of manufacture and assembly at this stage, which in turn goes hand in hand with cost optimization.
Let’s look at each of the points listed above in turn:
Mechanical structure
This houses the electronics, any hardware that needs to be enclosed, connectors, LEDs, speakers, wiring looms, and any other elements of the design that need to be protected, affixed, or covered. The shape of the product could ultimately be part of the brand recognition as people often associate different product designs to the brand (a good example of this would be the Dyson vacuum cleaner).
Key points to take into consideration while designing the mechanical structure are:
- Structural strength
- Product functionality
- Aesthetics
- Mechanical functionality
- Water proof, or dust proof (IPXX rating) requirements
- Life expectation of product
- Cost of manufacture (molding, casting, fabrication)
- Component count (Design for Assembly), combine two part or more, use snap fits, reduce fixings
- Material selection
Electronic design
The electronic design can be broken down into 6 design steps which are listed below:
1. Electronic specifications (made of a high level bloc diagram, expected electronic features, and main component selection): They provide the structure of the electronics, an initial material cost, and are used to estimate the cost of development (for both hardware and software).
2. Schematic design: It is the blueprint of the PCB design, connecting all components together to achieve expected functionalities. The schematic is used for simulation, and to generate the PCB and the BOM (Bill of Material).
3. Printed Circuit Board (PCB) design: During this step, the design must consider the sensitivity of power and RF circuits (including Wi-Fi, Bluetooth, GPS etc.). The tracks need to be carefully laid out and routing options analyzed to ensure the final design encompasses all the risk aspects. The design can be checked and verified to ensure the PCB matches mechanical requirements such as component position, screws, and other constraints. The PCB also has critical impacts on product radiation that are important to pass FCC and EMC requirements. Based on this, the designer gets Gerber files and a BOM that are used for manufacturing the PCBA (PCB Assembled).
4. Firmware: Most ‘smart products’ have various microcontrollers, including Bluetooth or Wifi chipset. The Firmware is low-level software used to configure the board to get all interfaces ready to be used by a user software or an app.
5. Prototype evaluation and debugging: This is where the first prototype PCBA gets tested and any issues found the need to be corrected.
6. Software: This is the application of the product: what the user will see, information to read, calculate, or display (screen, digit, sent to mobile phone).
Assembly
The PCBA controls the product and for an electronic product, this means providing the functionality to the product itself. If the product has motors, lights, pumps, etc, they need to be connected to the PCBA via connectors and wires. The wires’ specifications are to be determined by the amount of power they need to carry or the amount and speed of data transfer.
The connectors need to be selected based upon different criteria: do they need to be waterproof, dustproof, permanently connected or removed each time the product is used, the size of the cables, etc.
Hardware Requirements
When we talk about hardware, we are looking at motors, pumps, belts, fixing devices, lamps, LEDs, springs, etc… These will sometimes be off-the-shelf commodity items, and others will be custom designed to the product. Each item needs to go through a product requirement check in order to create a product specification – an example would be the screws used in the assembly: do they need to be tamper-proof, rust-proof, color-coded, or with other attributes?
This section of the new product development has its own detailed and in-depth process and will not be covered in the article. For more information of the NPD/NPI process check out this article.
User Interface (if required)
User Interface and User Experience (UI & UX): UI design focuses on end-user interfacing with the product (sound, screen…), whereas UX design refers to the user experience (buttons, easy to use and so on).
The UI has to be intuitive to the user, and at the same time the UX needs to give the user a sense of ‘this is easy’. Both these elements should interact seamlessly, giving the user a product that is great to use.
System Integration
The majority of today’s electronic products consist of multiple functional areas. Think of a vacuum cleaner that has the vacuum head, brush, and the bag (or bagless) compartment. Or think a simple blender, which has the base containing the motor and drive mechanism, the PCBA, the user interface, and then the (generally removable) top section where you load the contents to be blended.
All of these elements need to be integrated into a single finished product, and the interface between each element needs to be carefully designed to ensure full functionality and product specifications are met.
Material Consideration
Material selection is a crucial decision that needs to be made early in the design process:
- Will the product be molded, cast, fabricated?
- What does the product need to withstand from a user point of view?
- Are aesthetics more important than strength?
- Does it need to be waterproof, weather proof, chemical resistance?
These are just some of the questions the design team needs to consider when selecting materials for the product. Another factor is the quantity. If it is a high-volume product, then manufacturing processes need to be considered, as they will dictate to some extent what materials should be used. Likewise, if the product is a low-volume product, a different manufacturing process might be used.
Carbon bicycle wheels are light-weight premium products with high value. In contrast, aluminum wheels are heavier and much lower value. Both these products are bicycle wheels and do the same job, however, the material is very different, is the manufacturing process, and both have a market demand.
Safety regulations (RoHS, CE, FCC)
All products need to meet a certain level of safety, and these safety standards are often dictated by the country the product will be sold in. For products being sold in the USA, products may be required to pass FCC standards (this is for wireless products such as Bluetooth speakers). For Europe, a product will need to pass the respective CE standard before it can be sold.
Make sure the relevant standard is fully understood at the design stage so that key design aspects are included in the design.
How can I assess if a factory designed (ODM) product is compliant or not?
The bottom line is, you as the buyer are responsible for verifying the products you sell are safe to use. There are several steps you can take to check if products are likely to be compliant without sending them to an independent test lab:
1. Ask the supplier to provide test reports they have carried out on the product you are looking to purchase. These could be internal tests they have carried out or tests completed in local test houses. Note that the report should be genuinely done on the same product/version (including all components) you are planning to purchase. Any change, even minor, might cause noncompliance.
2. Ask for samples of the product so that you can do a thorough inspection of all the components and the workmanship. This will involve stripping down the product, looking inside, and checking component IDs. Examples of questions at this stage are; were the components assembled manually or repaired? Is the design well-structured, or does it look immature (not optimized)?
3. Test the product over and above the general working conditions it is likely to be used at. The objective here is to try and run reliability tests to stress the product the best you can without all the lab equipment.
4. You might have simple measuring equipment (e.g. multimeter, oscilloscope) that you can use to check current, amps, and other parameters. It is also good to check temperature with an infrared sensor to see if any electronics are overheating. Generally, good electronics don’t get over 70 degrees Celsius.
Having said all that, depending upon the country you are selling in, you will have to get the product tested and certified before importing it. Please check the regulations you must comply to.
How do you ensure that components, such as AC adapters and lithium batteries, are compliant?
In short, know your supply chain.
As mentioned before, you as the buyer are responsible for verifying the products you sell are safe to use. That said, there are steps you can take to reduce the risk of buying products that do not or will not meet compliance tests.
The safest way to purchase directly from the OEM manufacturer, who would be able to carry out test and certify their products, particularly if that OEM were an established brand such as TDK for power supplies or Samsung for battery cell.
The further away from the OEM in the supply chain, the greater the risk.
If you let your manufacturer buy from local suppliers, you need to ensure they are compliant with the strictest regulations. For example, lithium batteries should be at least UN38.3 compliant, IEC62133 is recommended, and the best would be to comply with American standards UL1642 and UL2054.
Another example: for AC adapters, it is better to keep your focus on UL and FCC approved products and avoid cheaper options (the risks are sparking at plug-in, lack of short-circuit protection, and so forth).
Are there any major technical differences between EN standards and, for example, UL standards that importers should be aware of?
The three main marks you will find on products are CE, UL, and FCC.
1. The letters CE means the product meets the European Union’s safety standards and other requirements for sale within the European Union.
2. UL means the product meets the standards developed by Underwriters Laboratories, a private safety testing organization in the USA.
3. FCC means the product meets the standards of the Federal Communications Commission, again in the USA.
CE vs. UL
The main difference between certification in the USA and Europe is that in the USA it is not mandatory to have your product tested and certified. With a few exceptions (with high safety risks), products can be sold without having the UL mark. In contrast, in Europe, it is mandatory to have the CE mark on a product before it can be sold.
The other difference is that the UL and FCC requirements state that a product must be tested by the UL Lab or another authorized third-party test house in order to pass and for the UL certificate to be issued. The CE regulations require the manufacturer to create a detailed technical file which includes tests they have carried out (either internally to the business or by using third-party test houses). Once they have documented the product is safe, they can prepare a declaration of conformity. In other words, the CE mark is self-certifying the product is fit for sale in Europe.
The declaration must include the following:
1. Manufacturer name
2. Product description
3. The CE mark directives that apply to the product, e.g. the machine directive 93/37/EC or the low voltage directive 73/23/EEC
4. The European standards used, e.g. EN 50081-2:1993 for the EMC directive or EN 60950:1991 for the low voltage requirement for information technology
5. The declaration must show the signature of a company official for purposes of the company assuming liability for the safety of its product in the European market
6. The EMC-directive (89/336/EEC) Electromagnetic Compatibility
7. The LVD-directive (73/26/EEC) Safety
FCC
The Federal Communications Commission (FCC) is an independent United States government agency that is directly responsible to Congress. The FCC was established by the Communications Act of 1934 and is charged with regulating interstate and international communications by radio, television, wire, satellite, and cable.
All devices that operate with an internal frequency of at least 9 kHz are required to test their product to the appropriate FCC Code. If the product is emitting radio frequencies (Wifi, BlueTooth,…), it needs an FCC ID registration (in essence, a permit to emit).
How does the software impact product compliance?
Software can have a critical influence on a product’s compliance. It is often the case where software limits the product from going beyond safe operating levels (this can range from speed, safety stops, temperature limitations, force, etc.)
Software (typically the firmware) is often adjusted to pass FCC or EMC regulations. In addition, software optimization can allow a significant reduction of power consumption, with potential benefits when it comes to marketing and product lifetime.
It is imperative that product regulations are deeply understood as early as possible in the design and development stages of the development process, so that a detailed product specification can be generated that the software development team can work against.
Once the software has been finalized and checked to ensure it controls the product as the specification requires it to, it needs to be digitally signed by the developer, along with the revision level and release date.
All software updates must be controlled by an Engineering Change Request process which includes controls for the approval, testing, verification, and release procedure.
About Sofeast Limited
Sofeast is an engineering, project management, and quality assurance firm based in Shenzhen, China. Sofeast works primarily for inventors and companies that develop their own products for manufacturing in China & Vietnam.
Sofeast engineers review designs and provide feedback that is often critical to not only pass certifications, but also ensure the product can be manufactured on budget, on time, and on quality.
Sofeast also develops prototypes of electronic and mechanical products, as well as small (pilot) production runs in order to complete process development and shorten time to market.
Learn more on the Sofeast website.
It is a very useful site for understanding the general approach to product certification.
Some of the standards and directives mentioned in your article need to be revised,
like EN 60950-1 which was replaced by EN 62368-1.
I did not understand why the declaration of compliance with a UL standard must be
conditioned by a listing and annual follow-up service of UL.
It is the responsibility of the manufacturer to maintain compliance. Isn’t it?