Planning to import sunglasses and other non-prescription eyewear to the United States? In this article, we explain what you must know about FDA regulations for sunglasses, and the OSH Act for safety glasses.
This guide also covers other relevant standards and regulations such as ASTM standards, CPSIA for children’s eyewear, California Proposition 65, and more.
Content Overview
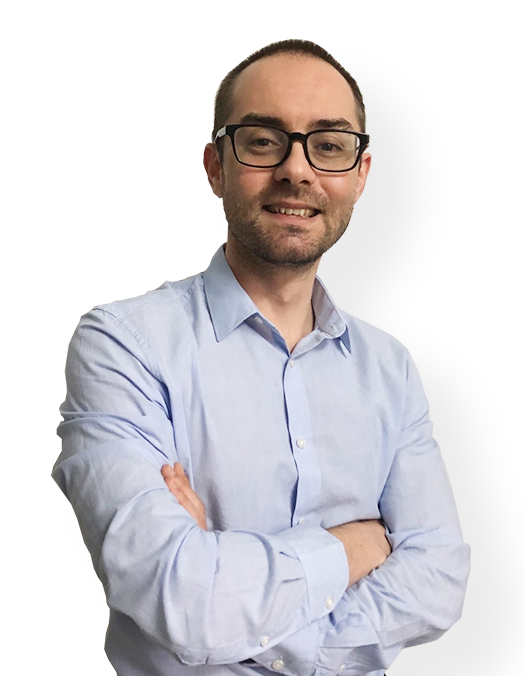
FREE CONSULTATION CALL (US, EU & UK)
- Request a free 30-minute call with Ivan Malloci to learn how we can help you with:
- Find product requirements
- Certification and labeling
- Lab testing
21 CFR (FDA): Sunglasses
Sunglasses, spectacle frames, spectacle lenses, and magnifying spectacles are categorized as Class 1 medical devices by the FDA. As such, covered products manufactured, imported, and sold in the US market should comply with the applicable FDA 21 CFR requirements.
This section explores topics such as requirements for registering sunglasses for sale, the quality system of such, and labeling requirements. We also discuss ANSI standards, lab testing, and risks.
Registration requirements
According to the FDA, eyewear importers and manufacturers should adhere to the following registration requirements:
a. They must register their establishment with the FDA. This process is known as establishment registration 21 CFR 807
b. Foreign companies must register their establishment with FDA and name a United States Agent
c. Manufacturers must list their devices with FDA
Also, sunglasses, spectacle frames, spectacle lenses, and magnifying spectacles are exempted from 510K Premarket Notification.
Device listing
The FDA requires that importers and manufacturers of sunglasses and other eyewear must list all the product categories and devices produced by the company.
They should submit the device listing to the FDA with the following information:
- Classification name
- Classification product code
- Title 21 CFR
Examples
Classification Name | Classification Product Code | Title 21 CFR |
Magnifying spectacles | HOI | 886.5840 |
Spectacle frames | HQZ | 886.5842 |
Sunglasses | HQY | 886.5850 |
Quality System Requirements
FDA 21 CFR also introduces requirements for current good manufacturing practice (CGMP). Those requirements cover the facilities and controls for, and the methods used in the following for all devices intended for human use:
- Design
- Manufacture
- Packaging
- Labeling
- Storage
- Installation
- Servicing
Subpart B of 21 CFR 820 – Quality System Requirements is divided into three main sections, namely:
- 820.20 – Management responsibility
- 820.22 – Quality audit
- 820.25 – Personnel
As an example, Section 820.20(b)(3) states that management personnel with executive responsibility should nominate – and record the nomination of – a management employee to be responsible for, and have established authority over
a. Ensuring effective establishment and maintenance of the quality system requirements
b. Reporting the quality system’s performance to management for review
Labeling requirements
21 CFR 801 lays out the general requirements for how medical devices should be labeled, including sunglasses.
We list below the information that must be included in your labeling:
- Company name
- Business location (street address, city, state, ZIP code)
- Statement (“Manufactured for…” or “Distributed by….”)
Note that appropriate statements such as “Manufactured by…” or “Distributed by…” must be included if the firm named on the label is not the manufacturer.
The regulation also specifies that the device’s label should clearly state – in easy-to-understand language – how the device is to be used.
Further, labels should not be misleading, and all statements on the device’s label must be displayed prominently.
Unique Device Identifier (UDI)
A unique device identifier (UDI) is a specific numeric or alphanumeric code that generally consists of two parts:
- Device identifier (DI)
- Production identifier (PI)
The DI section of the label is fixed and identifies who the labeler is, and the device’s version or model. The PI section of the label changes according to the device, and includes at least one of the following pieces of information:
- Lot/batch number
- Serial number
- Expiration date
- Date of manufacture
Certification
In accordance with 21 CFR 801.410, importers or manufacturers s are required to provide a certification statement.
We include an example statement from the FDA below:
“__________________________________” (Name of manufacturer or seller) hereby guarantees that the articles listed herein are impact-resistant within the meaning of 21 CFR 801.410 and have been tested pursuant to that section. Impact-resistant lenses are not unbreakable or shatterproof. Records of testing will be maintained for a period of three (3) years from the date of shipment, and copies will be forwarded to FDA upon request.
(Signature and street address of manufacturer or seller)
For more details regarding 21 CFR 801.410, you can read this document.
ANSI Standards
The American National Standards Institute (ANSI) oversees the development of voluntary consensus standards for products and services in the US. ANSI harmonizes US standards with international standards in order to facilitate the circulation of American products worldwide.
ANSI Z80.3 mandates that sunglasses manufactured, imported, and sold in the US must perform UV and visible light transmittance lab tests.
Lab testing
Companies such as QIMA offer lab testing services for sunglasses and other eyewear products, helping you confirm if your products are compliant with relevant product standards and regulations.
For example, according to 21 CFR 801.410, sunglass lenses should be impact-resistant in order to protect the user from a potential eye injury.
We recommend that you book lab testing prior to importing the products to the US.
Risks
Sunglasses manufactured outside the United States, for example in China and other Asian countries, are not by default designed to comply with FDA requirements. It’s therefore important to carefully select suppliers that have a verified track record manufacturing sunglasses and other eyewear for the US market.
Also, note that non-compliant sunglasses are frequently sold on dropshipping and other cross-border e-commerce websites. Do not assume that all sunglasses and eyewear available for delivery to the United States are ‘FDA compliant’.
OSH Act: Safety Glasses
The Occupational Safety and Health Act (OSH Act) mandates that employers must provide their workers with a safe working environment that does not pose serious threats to them and ensure the affected personnel’s physical safety at the worksite.
This includes providing the necessary protective equipment such as safety spectacles, goggles, or earplugs, to prevent the harms brought by chemical exposure, falls or any other hazards from using dangerous devices.
If you are importing eyewear for protection purposes to the US market, then your products are subject to the OSH Act.
The following factors should serve as parameters that determine the selection of protective eyewear equipment for employees on the worksite:
- Ability to protect against workplace hazards
- Fit properly
- Do not restrict movement and vision
- Be durable and cleanable
- Allow unrestricted functioning of any other required PPE
Product scope
The OSH Act regulates several types of eyewear, including
- Safety spectacles
- Goggles
- Welding shields
- Laser safety goggles
- Face shields
ANSI standards
The Occupational Safety and Health Administration (OSHA) requires that protective eye and face devices must comply with the ANSI/ISEA Z87.1 Standard: Occupational and Educational Personal Eye and Face Protection Devices.
ASTM Standards
In most contexts, ASTM standards are not legal obligations but optional guidelines that can help you to design a safer product.
In addition to the standards themselves, ASTM publishes detailed descriptions of testing methodology to guide you in ascertaining that your goods are as safe to use as possible.
Even if they might not be mandatory, adhering to ASTM standards benefits your business by helping to avoid forced recalls, which may occur even in the absence of a violation of mandatory safety standards should your product prove unsafe in practice.
Examples
- ASTM F803: Standard Specification for Eye Protectors for Selected Sports
- ASTM F659: Standard Specification for Ski and Snowboard Goggles
ASTM testing
A lot of the manufacturers in Asia do not have the proper assessment tools to conduct ASTM compliance tests.
Importers can hire a third-party lab-testing company such as SGS, Intertek, or QIMA to give their products an assessment report on ASTM compliance.
Other Regulations
Here we list other regulations that might be relevant for sunglasses and other eyewear.
Children’s Eyewear: CPSIA
Children’s products, including sunglasses and eyewear, sold in the United States must comply with the Consumer Product Safety Improvement Act (CPSIA).
Here’s a summary of the CPSIA requirements:
Note that the CPSIA doesn’t replace other product safety standards and labeling requirements in this article. For example, sunglasses must comply with relevant FDA rules, in addition to CPSIA.
Country of Origin
19 CFR Part 134 mandates that any product imported to the US from foreign or domestic manufacturers must be labeled with the correct Country of Origin mark unless an exception exists.
The mark must be placed in a conspicuous location of the product.
Examples
- Made in the USA
- Made in China
- Made in Vietnam
- Made in India
- Made in Thailand
California Proposition 65
California Proposition 65 regulates the concentration of hazardous substances in the products manufactured, imported, and sold in California.
California Proposition 65 currently includes more than 910 kinds of toxic or dangerous chemicals, and the list is still expanding every year.
Examples of restricted substances
- Phthalates (BBP, DBP, DEHP, DIDP, DINP, and DNHP)
- Nickle
Lab testing
Eyewear importers should hire a third-party lab-testing company for product compliance tests before mass import, which is often the only way to confirm the compliance of the products.
Most of the eyewear manufacturers in China and Southeast Asia are not able to provide the California Proposition 65 Lab test reports. We suggest you importers choose internationally-recognized lab-testing companies such as SGS, QIMA, Bureau Veritas, or similar companies.
The bare minimum cost of California Proposition 65 third-party lab testing is approximately $200, but it increases with the number of products, materials, and colored dyes that need testing.
For a large number of complex products, the total cost may be orders of magnitude higher.
Warning labeling
In some cases, instead of subjecting your product to California Proposition 65 third-party testing, it is permissible to attach a warning label to the product or its packaging.
When applicable, this is the only acceptable alternative to third-party testing.
Risks
Some plastics, coatings, paints, and hardware parts (e.g. hinges) used to manufacture sunglasses may contain excessive amounts of restricted chemicals and heavy metals. It’s therefore important to submit your product for third-party lab testing.
Further, many suppliers in the eyewear industry don’t have access to ‘compliant materials’. As such, limit your supplier selection to eyewear manufacturers with a proven track record (e.g. existing lab test reports) exporting products to the United States, and other developed markets.
Product packaging
In addition to ensuring the compliance of your sunglasses, importers and manufacturers should also pay attention to the product packaging compliance issue and also conduct the corresponding lab test for safety reasons.
Model Toxics in Packaging Legislation
Many states in the US set limits (e.g. 100 ppm) on the levels of lead, cadmium, mercury, and other heavy metals that packaging materials, dyes, and printing inks can legally contain.
SGS, TUV, QIMA, and other third-party testing companies offer testing of inks, dyes, and packaging materials for compliance with the regulations of each state.
Labeling requirements
Importers may also be required that the packaging conspicuously demonstrate any applicable compliance marks and/or country of origin along with other labels.
Bag suffocation warning
Bag suffocation warning label texts are mandatory for all Amazon sellers and in certain US states. In this article, we explain what you must know about creating warning label files, risks, and non-compliance penalties.
Here is an example of the warning (from Amazon):
Warning: To avoid the danger of suffocation, keep this plastic bag away from babies and children. Do not use this bag in cribs, beds, carriages, or playpens. This bag is not a toy.
Hi Ivan, how are you?
I’m an artist and Creative Director Based out of Miami, Florida. I make Eyewear in Italy through a factory near Modena.
I am looking to import my eyewear into the US.
I need a little guidance on the FDA process and basically logistics for bringing my Eyewear to the USA
Hello Marcel,
You can book a consultation call on the website if you want to discuss this further.